Share
Pin
Tweet
Send
Share
Send
Connection Methods:
- twisting;
-through the terminal;
-through the clamp;
bolt connection;
-soldering;
-through the tips.
Connection of wires by twisting.
This is the fastest and easiest way to connect one or more wires, so it is used more often than others. If you twist the wires correctly, then when using them in a home network with a small load, they will last a long time without reminders about themselves.
Frequent errors when connecting wires by twisting.
The most common mistake that installers make is twisting of wires of different metals (copper with aluminum). With such a connection, a complex electrolysis process occurs in twisting, which leads to the destruction of the metal itself. It is covered with oxides and potholes. All this leads to poor contact at the junction, and subsequently to heat. In the end, the conductors simply burn from each other. This is accompanied by the smell of burning insulation, crackling, and sometimes a fire.
How to make a twist of wires with different metals correctly.
Find a small piece of tinned wire
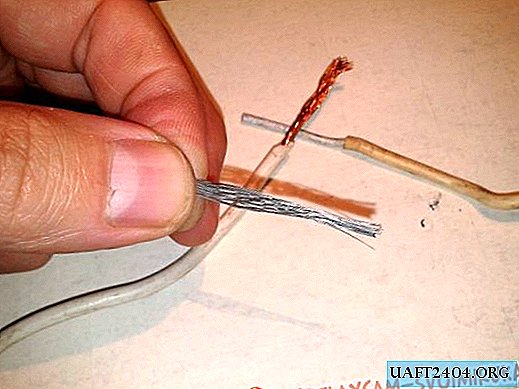
and remove insulation from it. Then fluff the cores and wind them evenly on an aluminum wire. With the help of pliers, with effort, wrap a copper conductor around it.
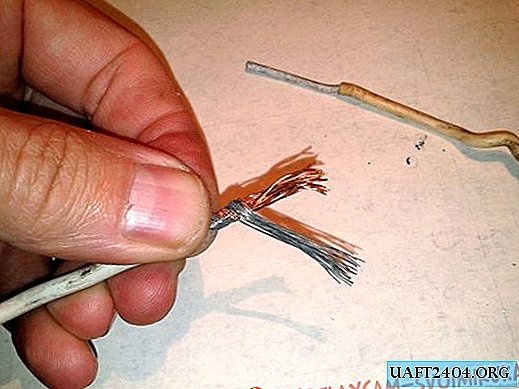
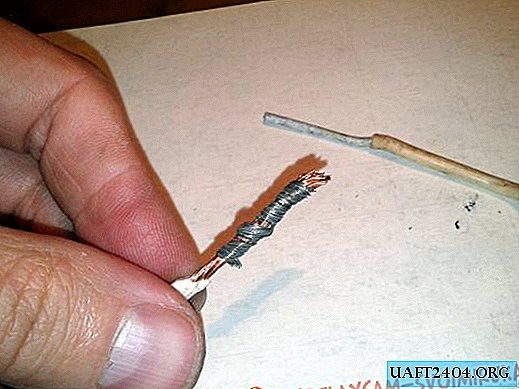
In the end, bend the excess to this twist.

Now copper is in direct contact with aluminum through a tinned wire. And this will not give rise to electrolysis on different conductors.
Connection via terminal.
The presence of terminals can also facilitate this work and ensure a good connection. There are many types of terminals, but they have the same principle. The photo shows two types of terminals, which can often be seen in different devices.

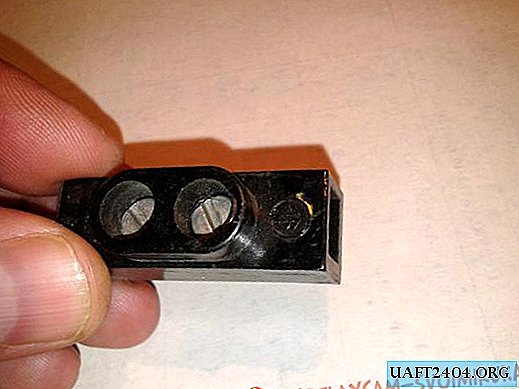
For example, in fluorescent lights, at the junction of the supply wires. Also, these terminals are freely available for sale and can be 10 pcs. and more in length. Having bought such a block, you can simply cut off the required number of elements with a knife. Connecting conductors of different metals in the terminal is not difficult. First you need to remove the insulation from the end of the wires by 3-4 mm so that the bare section does not go much beyond the terminal.
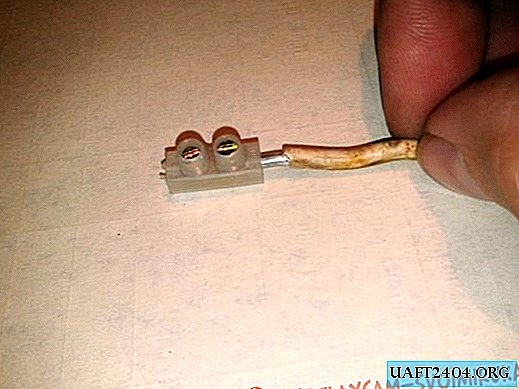
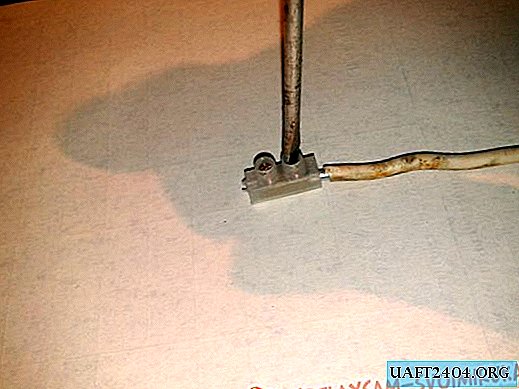
We turn off the screws until the wires of the wires pass freely, and after inserting, we clamp them.

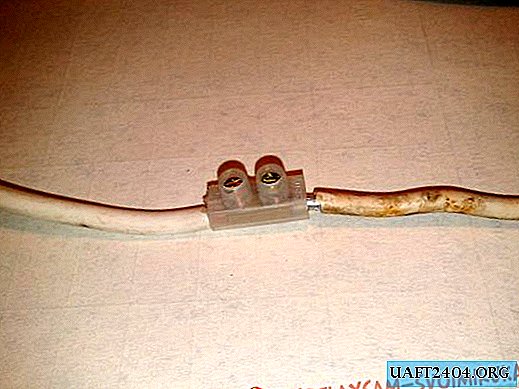
Do not make too much effort, otherwise the fragile thread will “break”, which will require replacing the terminal. This connection is pretty reliable. With a current of up to 1.5 kW, it is free to cope with its task. It all depends on which terminal to use. Here the weakest is considered, using a more powerful one, the flow current can be increased. In addition to the option to connect wires of different materials, the terminals can be successfully used to increase the length. This can come in handy when the wire in the box is so short that it is not enough to make a twist. This is where the terminal helps. The same applies to broken wires coming from the ceiling to the lamp. Incidentally, this is a very common problem. Even if a little conductor still sticks out from the ceiling plate, the terminal will successfully help to lengthen it.
Connection via clamp. Sometimes such or similar clip may appear at hand.

That connection problem can be solved using it. How to do this is clear from the photo.
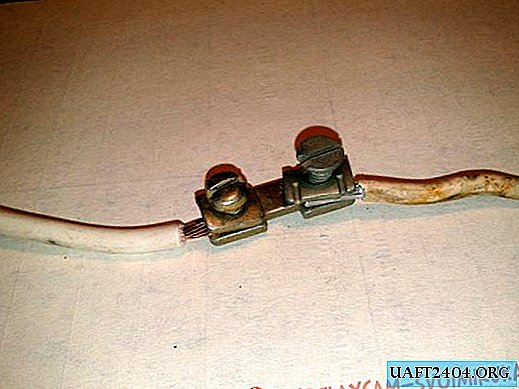

After the screws are firmly tightened, this entire exposed area must be insulated with adhesive PVC tape.
Bolted connection.
Bolts, nuts and washers are always at hand. Therefore, in the absence of clamps and terminals, they will also fit. By the way, on bolts of large sizes, they make rather high-quality connections of powerful cables of large cross section, and this method is still successfully used in industrial enterprises.
So you will need:
-bolt of the required length;
-nut;
-Three wide washers.
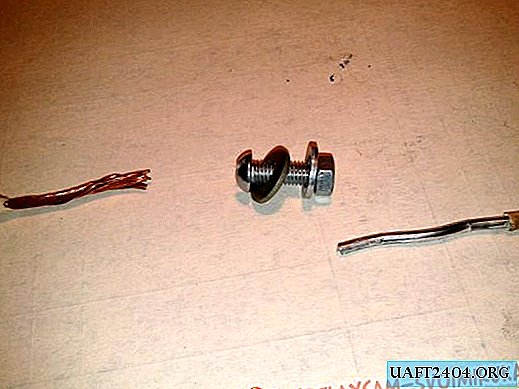
First we put one washer on the bolt, then we can make rings with pliers or simply wrap the conductor around the thread with pliers.


Bending is necessary by the movement of the thread. That is, so that when tightening the nut, the loop does not open to the sides.
The washer between the two conductors will not allow them to touch, and will prevent the effect of electrolysis, which destroys metals.

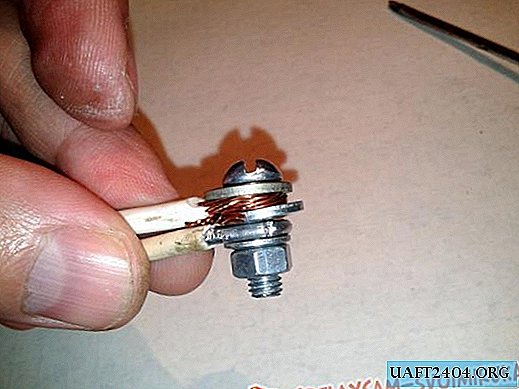
Soldering.
The solder connection is considered the most high-quality, since the resistance in this place becomes minimal. Some solder the twists in the boxes themselves, thus improving the connection. But this can be done with copper. And aluminum is not very well soldered. Yes, you can use different acids and additives, but they, as a rule, themselves destroy the compound over time.
But with the help of rosin and tin, you can tin the copper conductor. And then calmly twist it with aluminum. The connection will also turn out pretty high quality.

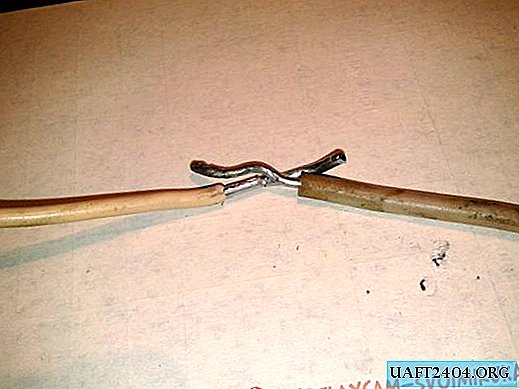
Tips.
If you find such tips, then it will be very good. This is one of the most reliable types of connection. We insert the wires into the lugs, and clamp them with pliers, and then squeeze the hammer and extension.

Tips should be tinned, or you need an aluminum conductor, wrap with a tinned wire before inserting into the hole in the tip. After the tips should be compressed with a bolt and nut, and isolate everything with tape.
Conclusion
Of course, now there are more advanced methods and devices for connecting wires, but they need to be bought and mastered, which takes extra money and time. The good old methods described above will be used for a long time, and will also serve faithfully for a long time. So why pay more ?!
Share
Pin
Tweet
Send
Share
Send